Costain - Precision Concrete Removal for Bridge Strengthening
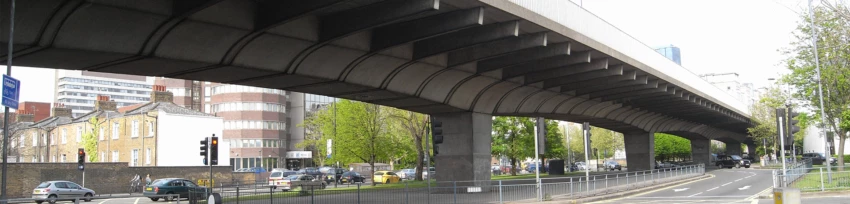
Precision Concrete removal supports strengthening of Hammersmith Flyover
- Customer: TFL / Costain
- Service: Concrete hydrodemolition and concrete removal
- Industry: Civil Engineering
RGL utilised precision hydrodemolition and surface preparation techniques during the strengthening of Hammersmith Flyover project; exposing bearings for replacement, scabbling areas ready for resurfacing and exposing steel reinforcements for bonding new concrete and coatings.
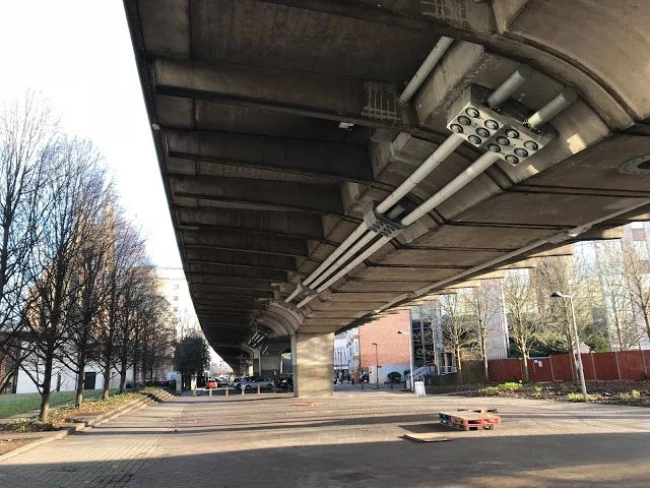
An inspection of the flyover discovered deterioration caused by water and salt from winter gritting leaking into the structure. This was corroding a number of the steel post-tensioning cables. Subsequently, a strengthening programme was initiated. The flyover opened in 1961 and carries the A4 over Hammersmith into London. It is used by over 90,000 vehicles a day.
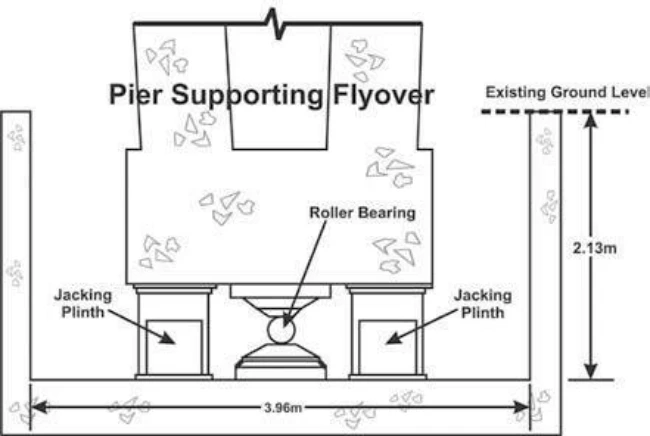
The project includes a replacement post-tensioning system, bearing replacement and a new drainage system, along with waterproofing and resurfacing of the whole 855-metre structure (including approach ramps). This project will prolong the life of the flyover and eliminate the need for major maintenance works for the foreseeable future. Transport for London (TfL) is managing the project as part of the Structures and Tunnels Investment Portfolio (STIP).
TfL awarded the final phase of the works to Costain who were tasked with strengthening all of the structure, and replacing the existing post tensioning strands with a new system. The bridge deck is supported on a single central row of piers comprising 16 spans – eleven at 42.7m long, two at 28.8m, two at 36.6m and one at 22.6m – giving a total length of 623m.

The works also include replacing the roller bearings on the 15 piers and the abutments, plus the expansion joints and the existing central reservation safety barrier along the length of the structure. Hammersmith Flyover articulates on a total of 34 roller bearings, two at each abutment and two in each bearing pit at the base of each pier, there are 15 bearing pits in total.
RGL were one of a number of hydrodemolition contractors approached to quote for the hydrodemolition works in December 2013. The initial tender requested a quotation for the removal of the top section, 0.70m, of bearing pit walls. The volume of concrete to be removed was approximately 3 m3 per pit, 45 m3 in total.
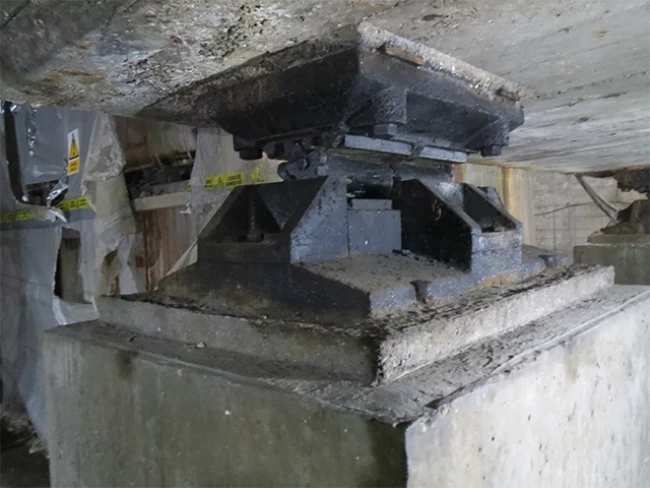
Hydrodemolition was the preferred method of concrete removal in order to preserve the existing embedded metal reinforcement bars and to reduce the risk of vibration that would have a damaging impact on the already fragile condition of the structure. This enabled the integrity of the remaining concrete sections of the flyover to be preserved.
RGL’s experience, developed over 25 years in the civil engineering industry, together with a knowledgeable, professional approach, produced a successful tender which proved to be both cost- effective and innovative.
Close negotiation and collaboration with Costain produced an increased scope of works greatly enhanced by RGL’s ability to offer concrete removal solutions applicable to the specific needs of the Hammersmith Flyover Strengthening Project. Our highly qualified and experienced operatives, and indeed all RGL staff, complemented Costain’s approach to working together in close collaboration and cooperation in all aspects of the project.
All RGL staff worked closely with Costain to meet their SHE requirements and attended daily morning site briefings. Team leaders also attended end of shift meetings and took an active role in the administration of Costain’s SHE requirements.
Working in close collaboration with Costain engineers resulted in the evolution of suitable protective working enclosures, acoustic attenuation and working platforms. This close cooperation greatly assisted with the task of removing resultant hydrodemolition debris from within the bearing pits.
RGL’s scope of work increased to include a number of necessary related operations, including removing and disposing of approximately 35 tonnes of contaminated water contained within the bearing pits. Thoroughly cleaning 50 years of accumulated detritus, grime and grease from the walls, floors, piers, and more importantly, the bearings was also involved. Once completed, the bearing pits were rigorously inspected in order for the next phase to proceed, – the more aggressive hydrodemolition.
Further operational activities associated with the Hammersmith Strengthening Contract are detailed below.
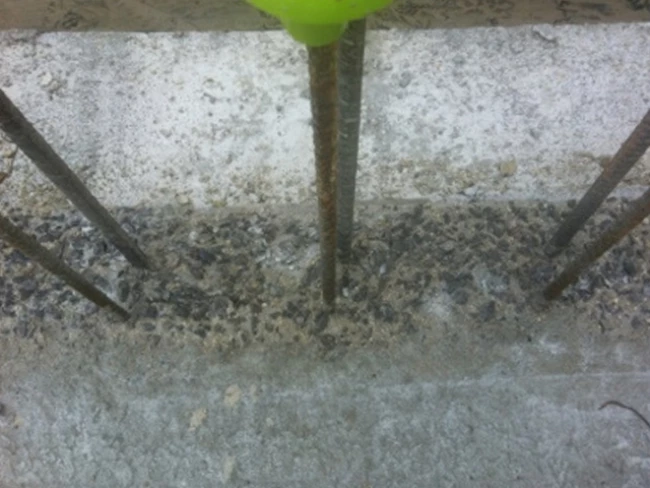
Ultra High Pressure UHP Scabbling
A number of areas of soffit required precise cutting to a predetermined depth. Our experienced operatives – together with Costain engineers – devised a working method whereby, working closely together, the desired results were achieved. The installation of the new anchor blocks necessitated the bonding of existing concrete with new. To achieve this end, the surface of the soffit required a relatively rough finish. Using a specialist UHP rotating nozzle, RGL was able to perform the ‘scabbling’ over the desired 166m2 area as specified. This is a fast vibration and dust free method of scabbling which greatly reduces the likelihood of bond failure.
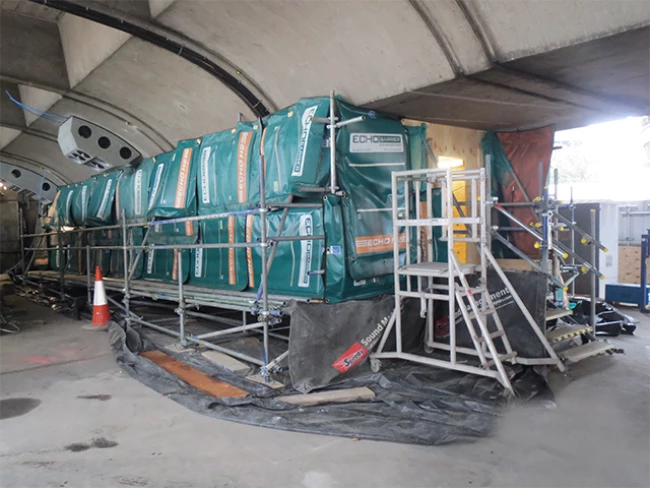
Anchor Blocks
The strengthening of the structure involves replacing the existing deteriorated post tensioning cables with a new system. In order to facilitate the installation of the anchor blocks associated with the new tensioning cables, the soffit of the flyover required hydrodemolition works to provide apertures to allow the passage of the tensioning cables. The total volume of concrete to be removed was approximately 9m3.
RGL worked with Costain engineers to produce diagrams illustrating the most desirable design for the scaffold access, working platforms and enclosures.
Tendon Anchor Blocks
With respect to installation of the anchor blocks, the scope of work, once again, increased to include the provision of 1,100 No. x 50mm diameter perpendicular holes through the 355mm thick soffit at precise intervals. Hydrodemolition was the chosen method, as it was imperative that the existing embedded reinforcing bars remained intact and undisturbed.
Parapet Joint Strengthening
The scope of work further increased to include the removal of concrete from joints within the parapet beam at 14 different locations along the east and west ramp parapet walls. The work required the removal of 14m3 of concrete, together with all waste water management within a 14 day period. Costain erected the working enclosures and the water containment bund to a specification and diagrams provided by RGL.
Bearing Removal
Finally, the flyover strengthening project provided an additional requirement.; RGL received instructions through an existing structural concrete contractor engaged upon the works. An order was issued to provide hydrodemolition services to remove a number of large concrete plinths that supported the existing redundant moveable bearings. The bearings were sited within a ‘confined space’ at both the east and west bearing chambers within the flyover ramp abutments. The total volume of concrete to be removed was 5.5m3.
RGL deployed a ‘confined space’ trained team for this aspect of the work.
RGL’s philosophy is to apply experience, competence and expertise to each job. Extensive training, innovation, collaboration and constant co-operation has provided, what we consider to be, a superlative service, utilising water jetting to assist with the Hammersmith Flyover Strengthening project.
If you would like to know more about our Precision Hydrodemolition services, Contact RGL today.
Request a call back